Here is a guide to evaluating the quality materials of an Chinese manufacturer like OPPEIN. This is important in the event that you're considering custom kitchen cabinetry furniture, wardrobes and wardrobes.
1. What materials are used?
To begin, familiarize yourself first with the materials used in furniture manufacture. For instance plywood, solid wood, MDF (medium-density fiberboard) particleboard, as well as laminate are the most popular options. Each has its own unique set of characteristics, advantages, and disadvantages. Solid wood can be the most robust, visually attractive and economical. Engineered wood products like MDF are more versatile and are less costly. Knowing what to look for can help you compare different manufacturers.
2. Verify the certifications
You should seek out certificates that demonstrate the safety and material standards. For instance, certifications like CARB (California Air Resources Board) compliance for formaldehyde emissions in wood products or ISO certifications that denote the quality of manufacturing management systems can be a good indicator of a firm's determination to produce safe and top-quality products. These certifications are often used to verify that the products being made don't contain harmful chemicals or are in compliance with international standards.
3. Examine the Wood Grades
Contact the manufacturer to inquire about the grade. Wood is rated by its appearance, durability as well as the intended use and other factors. The A and B grades will have fewer defects and knots, resulting in a better-looking finish. Knowing the wood grade will aid in determining the longevity and the quality of furniture.
4. Look at the finish of surfaces:
Surface finishes can have a huge impact on the longevity and appearance of furniture. The finish on the surface should be even and smooth and resist stains, scratches and moisture. To compare finishes, request samples and ask questions about the application method (e.g. curing times, multiple coats).
5. Review Hardware Components
Furniture hardware such as handles, hinges and drawer slides play an important contribution to the quality of furniture and its overall functionality. Take a look at the design and materials of the hardware. High-quality hardware should feel sturdy and operate with ease, as well as resist wear and wear and tear. Look for brands or specifications that have a reputation for reliability.
6. Learn more about the sustainability of sourcing and sustainable sources:
Examine the materials employed by the company. Sustainable sourcing isn't just good for the environment, but could also demonstrate a commitment to quality by the manufacturer. It is possible to inquire whether the source of the wood and also if it's from forests that are responsibly managed. Quality standards are often higher for manufacturers who prioritize sustainable practices.
7. Review Product Samples:
Request samples or models of furniture that you are thinking about. It allows you to inspect the workmanship and materials on your own. Be sure to pay attention to how the samples feel and how they weigh. The product must be sturdy and solid, without any signs of weakness or instability.
8. Test Procedures:
Find out if tests on the material are conducted by the manufacturer to determine the durability and effectiveness. Reliable manufacturers will often conduct tests to determine the wear resistance, resistance to moisture, and strength. Understanding their testing methods will help you feel confident to buy their products, because it demonstrates their dedication to quality control.
9. The transparentness of a manufacturing company's business:
A reliable company should be transparent about their products and production processes. They should be able give detailed information about their sources, materials and certifications. If a manufacturer is unwilling to share the details, it could be an indicator about the product's quality.
10. Consider Customer Feedback and Reviews:
It is also possible to look through reviews or testimonials left by previous customers. Comments about the material's quality and durability could give you an idea of what to expect. You can determine the credibility of a company by noting recurring themes, such as complaints about material quality or praise for the durability.
To conclude, evaluating the quality of materials produced by a Chinese furniture manufacturer such as OPPEIN requires an in-depth analysis of a variety of factors, including reviews from customers and certifications. The following tips will assist you in making an informed choice and ensure the furniture you purchase meets your expectations and the highest standards of quality. Take a look at the most popular wardrobe company for website advice including cabinet pics, kitchen units ideas, white closet armoire, luxury walk in closet, kitchen modern cabinet design, best kitchen cabinets, kitchen cupboard styles, black kitchen cabinets modern, design wardrobe, design cabinetry and more.
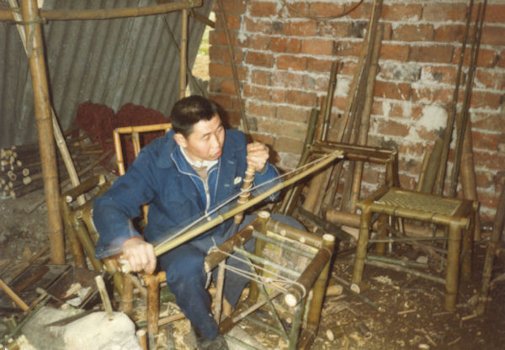
Top 10 Tips On Assessing The Lead Times And Capacity Of Chinese Furniture Manufacturers
This guide will assist you in evaluating the production and lead times of a Chinese furniture company such as OPPEIN. This is especially helpful when you are considering custom furniture, such as kitchen cabinets or wardrobes.
1. Request Specific Product Schedules
Begin by asking for detailed manufacturing schedules from your manufacturer. These should include timeframes for each stage of the manufacturing process starting from the sourcing of raw materials to final assembly and delivery. Knowing the timeline will help you evaluate whether their production capacity is compatible with the deadlines for your project, ensuring they can meet your specific needs.
2. Inquire About Standard Lead Times:
Request the manufacturer to give their lead times for different types of furnishings. The lead times for furniture can differ greatly dependent on the quality of the product, customization options, and order volume. If you know the average lead time for the products that you are interested in, you can better gauge whether they'll be able complete your order in a timely manner.
3. Evaluate the capacity to handle large Orders:
It is essential to evaluate the company's capacity to handle large orders. Particularly, if your undertaking is a big one, like outfitting a hotel or an apartment complex. Find out what their maximum capacity is for each type of product and determine if they are able to boost production during times of high demand.
4. Lead Time and Customization:
It is important to understand how the manufacturer handles this. A typical custom order will require longer time than regular orders. Transparency, reliability and honesty are displayed by a business that communicates the results of customizations on lead-times.
5. Flexible Production Scheduling
Ask the manufacturer if they are flexible with regards to changing schedules of production. Manufacturers may have to change their schedules quickly if the timelines of projects change. A manufacturer that is flexible enough to adjust the lead times and prioritize urgent orders is better able to meet your changing requirements.
6. Research Efficiency of Workflow and Processes
Examine the effectiveness of the manufacturing processes used by the company. Ask about their workflow, automation, and any processes that they use to make their products more efficient. An enterprise that employs efficient processes and modern technologies will likely have lower lead times and greater production capacity, which will improve your overall experience.
7. Verify the backup production capacity:
In the event of an unexpected issue such as equipment malfunction or supply chain disruptions It is crucial to have a contingency plan in place. If they've got backup capacity for production or other material suppliers, ask them. A company with a solid contingency plans will be better prepared to deal with unforeseen issues and not affect the lead time.
Check the performance metrics from the past
Request information from the manufacturer on their performance over time in terms of lead times and capacity for production. This could include information on the average lead-times for different kinds of products, their on-time delivery rates, or any historical trends regarding production capacity. Analyzing this information can give you insights into their reliability and consistency over time.
9. Examine Communication During Production:
Communication throughout production is essential. Check with the manufacturer to find out how they update customers about the status and progress of their orders. This is particularly important when there are delays or adjustments to lead times. Open communication from a manufacturer will show a commitment to quality service and allows you to keep your expectations in check throughout the entire process.
10. Request references from former clients:
Request references from past clients who worked with the manufacturer on a similar project. Find out about the experience with lead times and production capacities. Positive reviews about the company's reliability can assist you in assessing the company's ability to meet your deadlines.
In conclusion, assessing lead times and production capacities of a Chinese furniture manufacturer like OPPEIN involves a thorough analysis of production schedules. Flexibility, process efficiency and feedback from customers are essential aspects to be considered. You can ensure that the company meets your needs and deadlines by following these guidelines. Take a look at the top rated wardrobe companies for website examples including build kitchen cabinets, top kitchen cabinets, kitchen cabinet companies near me, kitchen cupboard styles, cupboard kitchen cabinet, purchase kitchen cabinets, white shaker cabinet kitchens, white modern kitchen, style of kitchen cabinet doors, melamine kitchen cupboards and more.
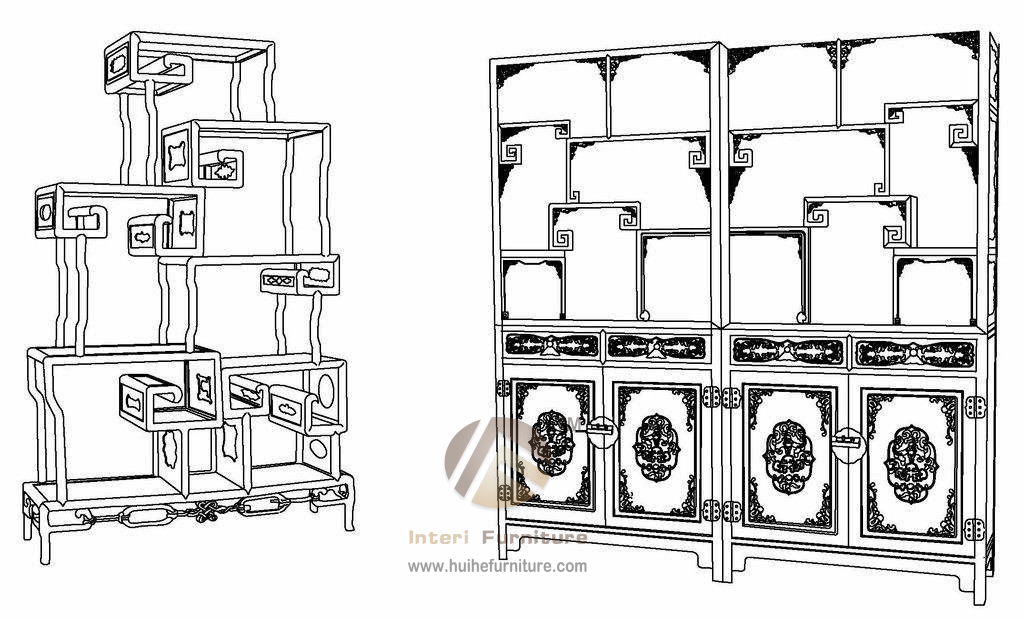